【執筆者情報】
芝田 稔子(しばた としこ)
物流専門のコンサルティング会社 湯浅コンサルティングのコンサルタント。
物流のムダ、在庫のムダをなくし、企業の収益率を向上させ、地球環境をよくすることを目指し、多くの物流事業者、荷主企業の支援を行う。
適正在庫ってなんだ?
この連載は、初めて在庫管理を担当することになった若手社員「倉之助くん」を主人公に、困ったり、迷ったりしながら、在庫管理を学んでいく姿を紹介するものです。
読者の方々には、倉之助くんに共感したり、同情したり(?)しながら、在庫管理について学べるものにしたいと考えています。倉之助くんの奮闘を楽しみながら、応援して頂ければ幸いです。
※「倉之助くん」は、2023年1月16日に出版された「手にとるようにわかる在庫管理入門」に登場するキャラクターです。
前回、倉之助くんは、上司から「究極まで絞り込まれた在庫の姿とは?」という課題を与えられ、在庫は何のために持っているのか、在庫を置くべき拠点はどこか、デポや工場倉庫など拠点の性質により在庫の持ち方は変わるのか、など色々考えてみました。
顧客への納品を担っているデポで働く友人や工場倉庫の先輩などにもヒアリングを行い、「在庫は顧客に納期を守って納品するために持っている」ことや、「工場倉庫の在庫は生産制約の影響を受ける」ことに気付きつつ、「究極に在庫を絞り込んだ姿は明日の1日分である」という仮説にたどりつきました。
さて、この仮説は正しいのでしょうか。
意識すべき「1日分」と「リードタイム日数」
倉之助くんは、「出荷1日分」を意識して出荷状況、在庫状況のデータを見てみました。倉之助くんが考えた「究極に絞り込んだ在庫量=出荷1日分」で物流拠点を運営することはできるのか、考えることにしたのです。
以前調べた「最高のステーキソース」は、ほぼ「1日1個」出荷されていました。明日の出荷に間に合う量が最小限の量であるならば在庫量は「1個」でいいはずです。
しかし、実際にはこの商品はたまに欠品して、営業時代の倉之助くんは顧客に謝罪していた経験がありました。
倉之助くんはデポにいる友人に状況を確認してみることにしました。
「最高のステーキソース」の在庫はどんなふうに管理されているの?
あれは単価が高いから、たくさん在庫しないようにすごく注意しているんだよ。
在庫が3個まで減ったら5個発注しているんだ。
スペシャルケアをしているせいかドヤ顔です。倉之助くんも一応賞賛しつつ、、
丁寧にチェックしてるんだね!
でも、工場倉庫からデポ(物流拠点)への補充は基本的に毎日行われているよね。
3個ある時点で発注しているのなら、欠品が起こるはずはないと思うけど、
実際は欠品が発生することがあるよね。この原因は何なんだろう?
実はこの商品は他のメーカーからの仕入れ品なんだ。
注文したら2日後に届けてもらう約束なんだけど、
たまに遅れることがあって困るんだよねー。
とはいえ、発注点を引き上げると、在庫量が増えちゃうので、それは避けてるんだ。
※「発注点」とは、発注すべきタイミングのことです。
倉之助くん、究極に絞り込んだ在庫を「出荷1日分」として捉えることは有効かもしれませんが、それだけではダメなのだなと考えました。
発注してから2日、3日とかかる場合、そこで需要が少し上ブレするようなことがあれば、欠品が発生してしまうことになります。
「注文してから何日後にその在庫が使えるようになるのか」
(これは発注リードタイムと言われる日数です。取引先ごとや商品ごとに異なる場合があります)アイテムごとにすべて把握しておく必要がある。
よく言われる「適正在庫」って何?
倉之助くんは究極に絞り込んだ在庫量は「出荷1日分である」という考え方と、リードタイム日数を把握して在庫を絞り込まねばならないということを上司に報告しました。
上司はその報告に納得してくれたものの、さらに倉之助くんを悩ませる質問をしてきました。
その「1日分」と、巷でよく言われる「適正在庫量」とはどういう関係なの?
あらゆる拠点で「1日分」とリードタイムを考慮した在庫量をプラスすることで管理できるの?
倉之助くんは工場倉庫にいる先輩の言葉を思い出しました。
デポに向けて出荷するために必要な量といえば、確かに明日の1日分ではある。
でも、工場倉庫にはデポと違う種類の在庫がある。
工場からできあがったものが送り込まれてくるんだよ。
これは生産都合で送り込まれてくるから、倉庫側では管理が難しい。
工場倉庫では、工場での生産の影響を受け、出荷量1日分に絞り込めない理由があることになります。
また、デポ吉くんの「3個まで減ったら5個発注」という発注の仕方も気になります。なぜ5個発注するのか聞いたところ
そりゃあ調達元のメーカーから、5個以上で発注するよう言われているからだよ!
謎にドヤ顔で答えてくれました。
生産の都合も取引条件も簡単に変更できるものではありません。在庫量を「1日分」に抑えようとしても、現実的に実現可能な最小の在庫量は、これらの制約に対応した量ということになります。
最小生産ロットなどの生産の都合により発生する在庫量、
調達ロットなど取引先との取引条件により発生する在庫量が、
「出荷1日分」の量よりも大きい場合、
在庫量は「1日分」まで絞り込むことはできない。
このような生産や調達の都合、在庫量に影響を与える条件は「制約条件」と呼ばれます。これらの制約を考慮したうえでの最小の在庫量が、現実的に絞り込み可能な在庫量であり、これが「適正在庫量」です。
在庫量を適正に維持するには?
「適正在庫量」について、しっかりと自分の頭で考えた倉之助くんは得意顔で上司に報告しました。上司は褒めてくれたものの、また質問が出ました。
なるほど!
制約条件をそれぞれ確認して、それだけを持つようにすれば、
現実的に可能な「究極に絞り込んだ在庫」が実現するわけだね。
では、その状態をどうやって維持すればいいんだい?
倉之助くん、自社の在庫管理システムを見てみましたが、在庫量を確認することはできるものの、「この在庫はいくつ持つべきとか」、「そろそろ発注しないと欠品する」といった情報は見つかりませんでした。
デポ吉くんや工太先輩は、このシステムを使って、どのように在庫を管理しているのでしょうか。聞いてみると、それぞれExcelを駆使して発注量を計算しているとのこと。
(重要な情報が?!)どんな計算式を使っているんですか?
実は二人とも発注のたびに迷いながら数量を決めており、、、
結局のところ“KKD”
KKDと言うとかっこよく聞こえますが、実は「カン・経験・度胸」の頭文字をとったもので、まったく論理的でもないし根拠もなく、どう考えてもかっこよくありません。
デポ吉くんがExcelを使っているのは、商品ごとに前にいくつ発注したかすぐわかるようにするためで、いわばメモ帳代わりでした。Excel好きな倉之助くんとしては、ややショックです。
工太先輩は欠品を防ぐべく、商品ごとに在庫の推移がグラフで見えるようにExcelを使っているのですが、出荷状況が様々に変化するので、いくつもの商品を管理しきれていません。
これではまずいだろうと、倉之助くんは買ってあった在庫管理の本を見直したり、インターネットで検索したりしてみました。すると、「発注方法」というのは古くから研究されており、今は4つの方法に集約されているという情報にあたりました。
在庫量を必要最小限の量に維持するための計算式がある。
倉之助くん、デポ吉くんや工太先輩の悩みを解消できるかもしれません!
次号へ続く…
芝田さん著書の「手にとるようにわかる在庫管理入門」がかんき出版より発売されました!
豊富な図解で初学者に最適!なのでぜひ手に取ってみてください。
物流や在庫管理でお悩みの方、まずは気軽にご相談ください!
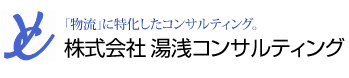
株式会社湯浅コンサルティングは、「物流」に特化したコンサルティング会社で、物流の改善、見直し、在庫削減、物流ABC導入など、30年以上の実績があります。調査研究の受託、物流管理ソフト開発支援や、物流人材研修の場への講師派遣を行うサービスも行っており、物流に関する著書も多数出版しています。